A friend offered me a truck that he’s had on his TODO list for over 20 years. This truck has been sitting in his car-port, covered in various bits of detritus. After almost an hour of excavation, I was finally able to see the truck. Code-name: Terrible Idea.
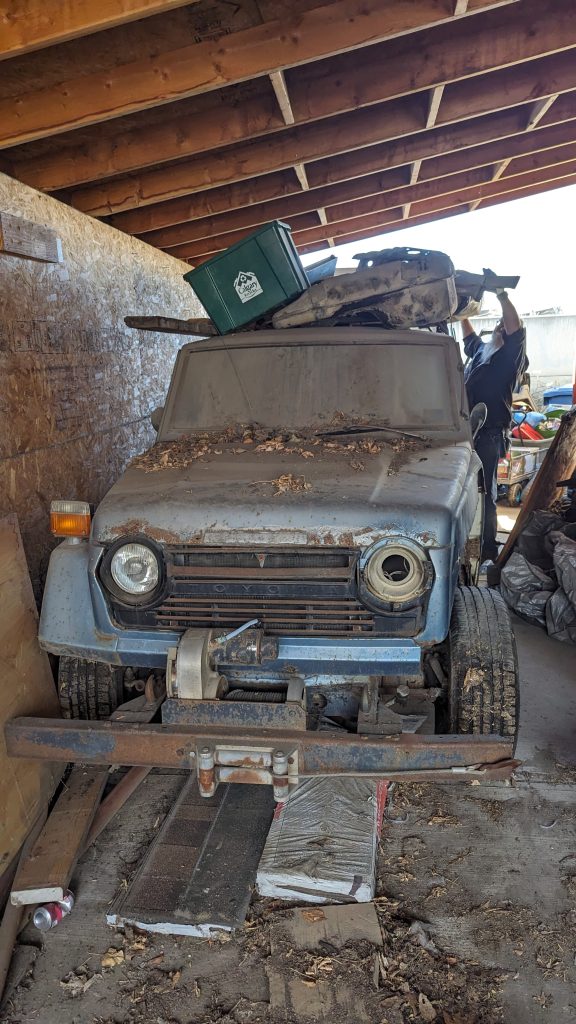
What are my plans for it? I’ll save that for a later post because I’m not entirely clear yet. First order of business is to deal with rust and missing metal. Its biggest problem is the A-pillars that the front doors are mounted to are completely rotted.
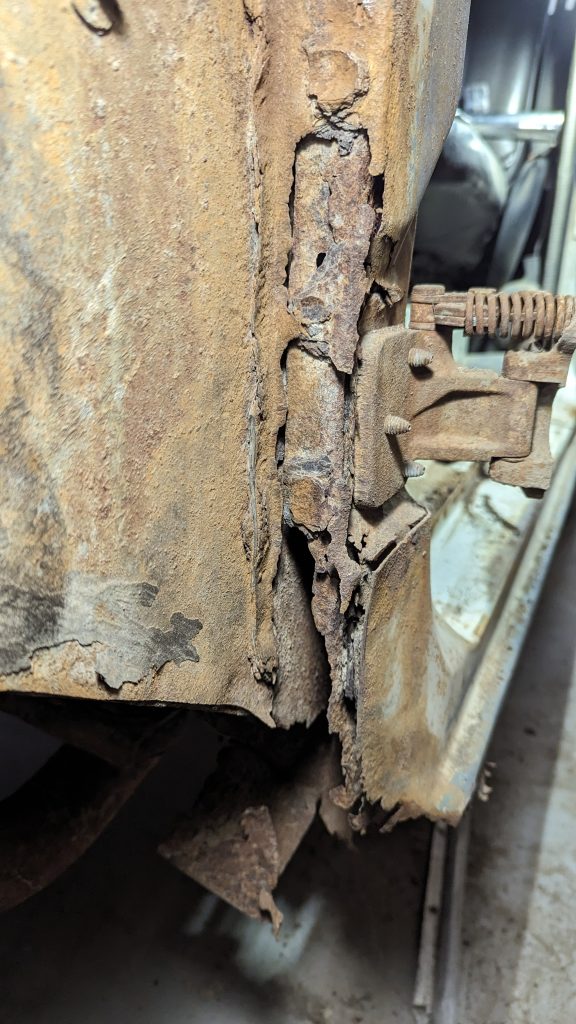
The first decision I’ve made is not to do a museum level restoration. I want a truck that looks cool and still looks like an FJ-55 but a purist would immediately know something has been done to it.
First order of business was to tackle one of the A-pillars to see how doable it is. If those are too difficult, then the project is a no-go for me. Fortunately, they proved doable given the technology I possessed. I built the A-pillar out of some 2x3x.188 rectangular tubing. I mated it to some 1.5x3x.250 rectangular tubing to replace the almost completely missing rocker panels. I did a floor patch while I was in there. Lots of spot welds to drill out. Not sure I’ll go to that extend on the passenger side.
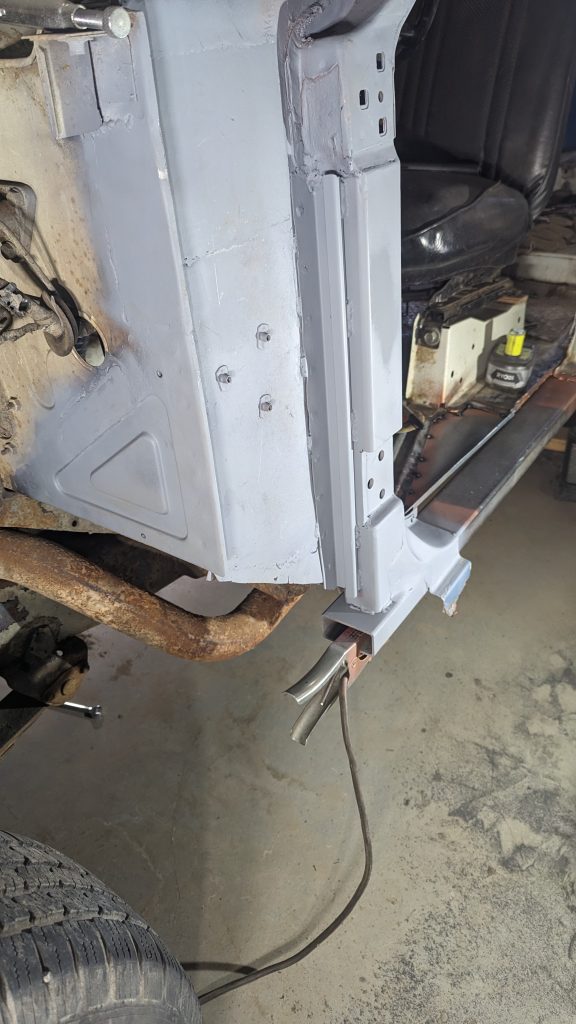
The drivers side front door mounts perfectly and lines up nicely and opens/closes cleanly. This project has now passed the ‘doable’ gate.
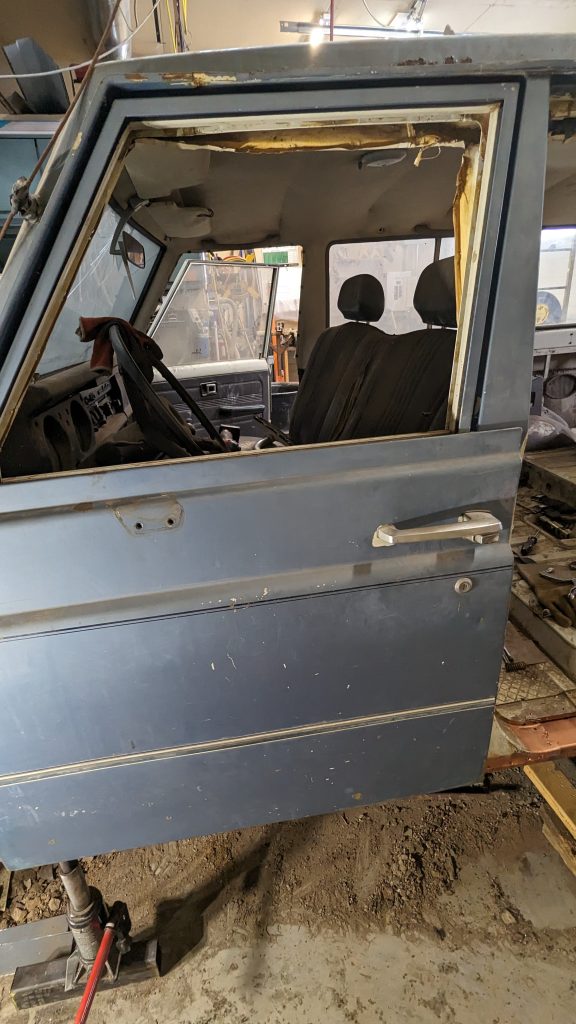
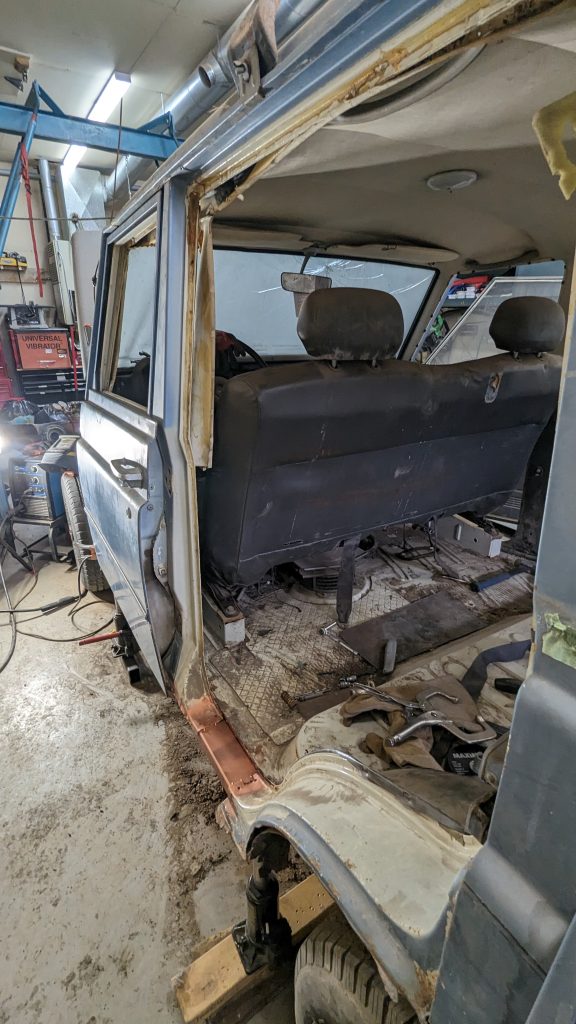
Next order of business was to dismantle the interior and build a rotisserie.
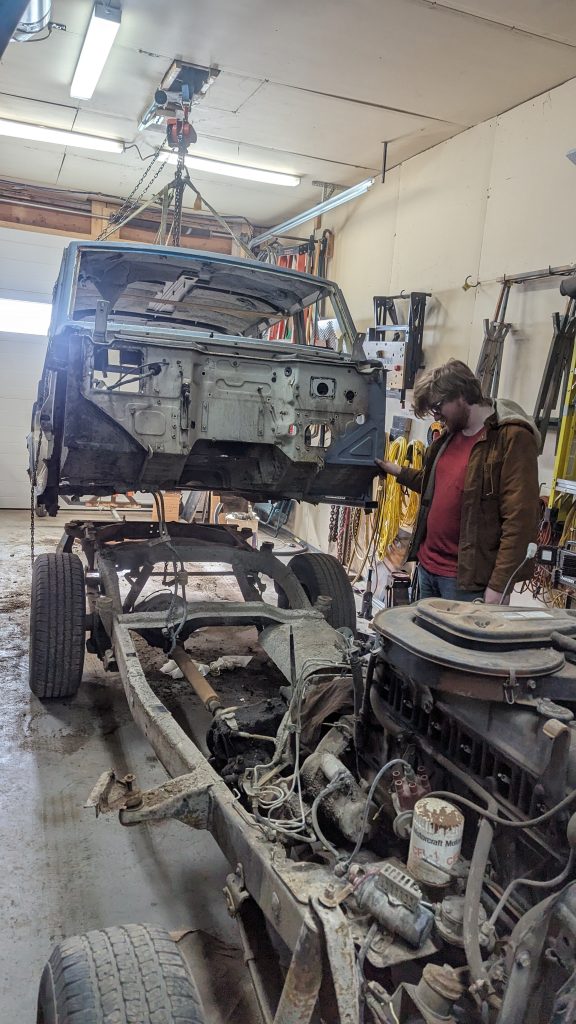
